Implementing a Lean Labor Strategy
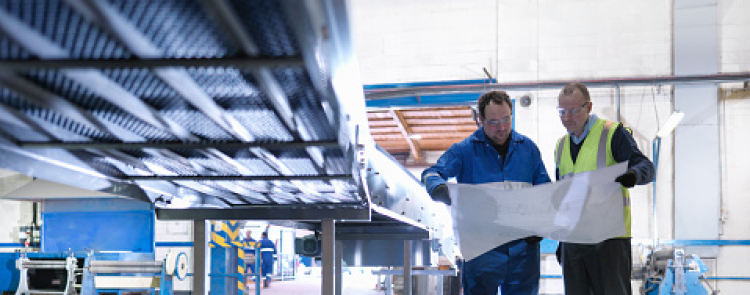
How do I align my skilled labor with real time changes in demand? How do I utilize labor as a source of competitive advantage? How do I align training programs to maximize productivity? These are questions any manufacturing organization should ask and take action to address.
Gregg Gordon describes Lean Labor Practices in this article on Manufacturing.net.
He states, “It is important for manufacturers to increase productivity, control costs and optimize labor resources and align them to the most important project or goal. Conceptually, all of this sounds good, but for many manufacturers, the question remains: How?”
Manufacturers often find themselves with incumbent skill sets that have been formed to a particular process or processes over time. This allows them to operate effectively in a static environment with a predictable set of obstacles. However, inefficiencies are exposed when change is implemented. Sure, some of this is unavoidable, but hiring and training the right skills sets will allow greater flexibility when adapting to market changes in demand.
Scientific Management Techniques’ skill assessment and training programs allow manufacturers to acquire/develop the skill sets needed to implement a lean labor practice.
SMT’s Validated, Hands-On Selection-Evaluation program, using portable assessment machines and a non-written, non-verbal, task-oriented methodology, identifies the most skilled, most capable, and most trainable candidates and incumbents. It solves the question of who needs what training, eliminating wasted time and cost.
Here are some of the ways in which the assessment program can be used:
- In the hiring process; to identify and measure the skills required to operate, maintain, and troubleshoot a manufacturing facility.
- For promotions; using the assessment program ensures you promote the most skilled incumbent.
- To identify skill gaps/training needs. When you assess your workforce you identify the “specific” training needs of all employees. With this data you can deliver highly targeted training.
- To measure the effectiveness of training delivered.
SMT’s Industrial Skills Training curriculum is a 100% demand-driven program. It is highly customizable to fit only the specific needs of the client utilizing well over 200 training aids. This curriculum has been built by and for industrial operations professionals over the last 40 years.
Gordon summarizes, “While it is true that it is extremely tough to compete in the manufacturing industry today, Lean Labor can help. With Lean Labor, manufacturers gain a proven way to gain new efficiencies, reduce and control costs, and increase overall productivity. In turn, this allows them to focus on revenue-generating activities, strengthen the bottom line, and increase their overall competitive advantage.”