Solving a Crisis: Closing the Manufacturing Skills Gap
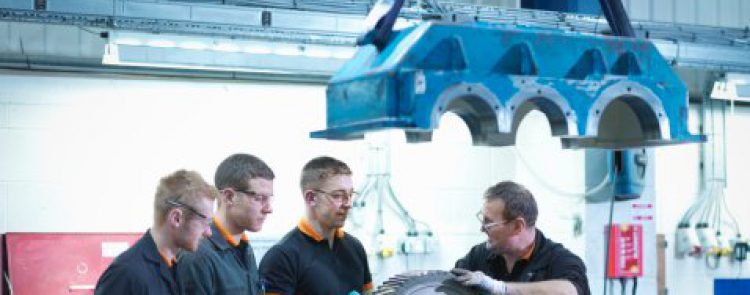
The Manufacturing Skills Crisis: There is a lot of benefit derived from raising awareness of the problem. Unfortunately, as the data indicates, that problem is only going to get worse and reversing decades of negative information and influence over manufacturing is not going to change quickly. Here are some grim facts that Frank Cavallaro of ebnonline.com points out from a recent study done by Deloitte and The Manufacturing Institute:
- Six out of 10 manufacturing positions remain unfulfilled because of the talent shortage.
- 82% of executives say the skills gap will impact their ability to meet customer demand.
- 78% of executives indicate it will be hamper their ability to implement new technologies and increase productivity.
- Two million workers will be needed to cover the projected shortfall as only 1.4 million out of 3.4 million positions are expected to be filled over the next decade.
There is a solution to curtail the problem immediately. At Scientific Management Techniques, we implement a 2 part, Hands-On manufacturing skills program that helps manufacturers and community colleges to address the manufacturing skills shortage. Fortune 500 manufacturers have been using this solution for decades including Unilever, Diageo, P&G, Mars/Wrigley, Reckitt Benckiser, Coca-Cola, Cummins, Merck, Alcoa, AstraZeneca and many more.
It utilizes one of a kind, Hand-On Assessment Machines to identify manufacturing skill sets both for hiring and for identifying skill gaps/training needs. The efficacy of the assessment program has been confirmed by over thirty validation studies conducted by Industrial/Organizational PhD’s and by over forty years of success driving productivity in the field. Here are a few of the benefits of the assessment program:
|
|
The second part of the skills program includes a 100% demand-driven curriculum. The curriculum has been built by and for industrial operations professionals over the last 40 years. It involves over 200 Hands-On training aids and a curriculum that is constantly evolving to meet the needs of industrial clients.
Put these two unique solutions together and any manufacturing community or stakeholder can solve their skills shortage.